

The CAM is doing all the trig and calculus and not the control. Set up changes, then the program needs to change to match. Without DWO/TCPC you are at the mercy of your set up. If you want one work offset for the whole program then you need to know the center point of rotation, and there is a bunch of ways of programing that. This can actually be the most precise way to program 3+2, but obviously much more set up and room for dicking things up. If every rotational position is taught as a separate work offset relative to features on a part, then the center of rotation is worthless. With positional you don't need to know the center of rotation depending on how you program. For one there is 3+2 (3 full/simultaneous, 2 positional), AKA 5 axis positional, and full 5 axis (5 simultaneous). (Haas is basically playing catch up with what other manufacturers have had for years, Haas just markets things 100 times better than any other machine tool manufacturer). Whether your control is capable of either DWO or TCPC/TPC is for you to find out. Hope this makes sense, it's been a few years since I did it and it was a first time experience for me.įanuc has had dynamic work offsets for probably a decade now. It was always a couple thousandths off, and that deviation from X+.102 would be the amount the EXT Z coordinate was moved. 002" shim, so if the face of the platter was exactly on the swing point, the position display would theoretically display X+.102. at B90, touch off the side of the platter with the side of the gage pin.

Using a known length and diameter tool/standard/probe (gage pin in a tool holder), touch off the face of the platter in Z, set EXT Z0Ħ. Sweep bore in platter face at B0 to set EXT X0/Y0 (or G54, etc, we used EXT so all the other systems would be 0)ĥ.
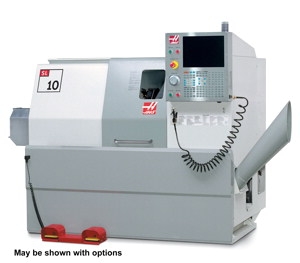
Rotate to B90 to check for squareness, if something is off something is really wrong.Ĥ. Still not sure it was the correct way to do it.ģ. Indicate/sweep on platter face at B0 (parallel with table) to set rotation zero - IIRC this was a machine parameter and we had to cycle power/recheck. Align trunnion casting to Y-axis and clamp to tableĢ. Again, this was on a VMC that had a separate trunnionġ. I can tell you the procedure I used on the Kits to set the swing point, or at least the basics since some of the details may be different with your machine. Wish I had something more helpful than that, hopefully someone with a better grasp on it will be along shortly. Then, set up the work system in your CAM software to be aligned with that feature (may be a lot easier said than done). View QuoteAFAIK it should be possible but how to go about it on a Fanuc I can't say.If there's any established features already on the part, you can try to locate off of one of those, or indicate the part in and try to get that feature coincident with the center of rotation.
